The Swiss government’s target of reaching net zero carbon emissions by 2050 is a necessary aim – and one that poses major challenges for the building industry. Overcoming those challenges will require shifting away from the linear paradigm of extract-build-discard and adopting circular principles, where used materials are given a fresh life.
Sizeable scope for making a positive impact
The building industry – including both the construction and use of buildings – accounts for 25% of Switzerland’s carbon emissions. It’s also a heavy consumer of energy and raw materials: some 30% of the energy and 40% of the natural resources used in Switzerland each year are attributable to buildings. This industry also generates 18m tons of waste per year, or 80% of the country’s total.
Some 80% of Switzerland’s buildings date from the last century. So now it’s time to think carefully about how these buildings should be renovated. If we’re to meet Switzerland’s net-zero target, 4% of those buildings will need to be renovated annually – yet we’re currently inching along below 1%. We desperately need to increase the pace of renovation, and circular principles can be a decisive factor in making those renovations more efficient.
Circular thinking means more than just recycling
Many people mistakenly equate the circular economy with recycling. The concept actually extends much further, encompassing three main strategies:
- designing and using products in a more intelligent way
- extending the lifespan of products and components
- making effective use of secondary raw materials.
What that means in practice
For renovation and extension projects, adopting a circular approach means taking several concrete steps to ensure resources are used sustainably. First, a full audit of the existing structure and materials is performed to identify all components that can be reused, thus reducing the need for new materials. This includes assessing the building’s interior and exterior and deciding which materials can be reused on-site or sold on a secondary exchange. Energy audits are then conducted, along with a review of the building’s other systems to check their performance and compliance with the latest standards. And during the design phase, modular features and recycled materials are factored in from the outset, for enhanced flexibility and a smaller carbon footprint.
Taking such steps can deliver major environmental benefits. For instance, waste can be reduced by as much as 60%, shrinking the volume sent to landfills and cutting waste management costs by 10%. A circular approach can also lower carbon emissions by 30% and, thanks to the use of secondary and recycled materials, slash resource consumption by 40%. All this translates into more sustainable construction processes and buildings.
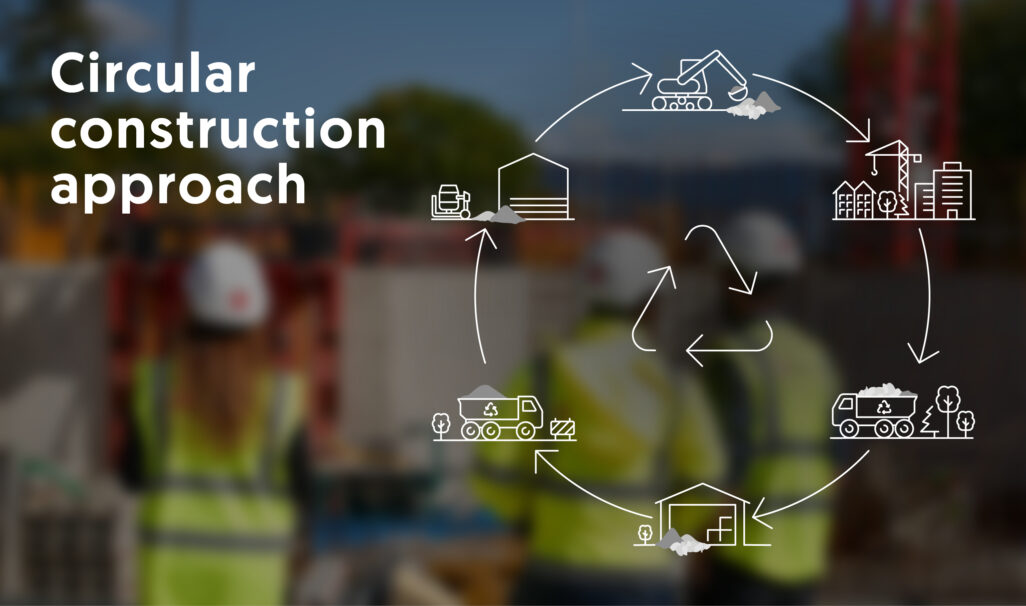
Worth the effort
Embracing circular principles in the building industry will require rethinking our current approach. We’ll need to adopt a holistic view that incorporates social, economic and environmental considerations. Such a shift can go a long way towards cutting carbon emissions and spur the development of more efficient technology. But we’ll need to change our standard practices and address sustainability as early as possible in the design process.
Interested in this topic? Fill in the form below and we will contact you to talk about your project.